This month, our Sensible Semiconductor News Update will explore myths that have sprung up in the microelectronics industry about the nature of 3D flash memory, some tips to help organizations lower the costs of doing business through improvements to how they manage their inventory, and new efforts to “go green” by coming up with an eco-friendly approach to PCB design.
Keeping Up With 3D Flash Memory
Flash memory innovator KIOXIA first introduced 3D flash memory in 2007 as a layered evolution of its original flash memory invention. By vertically stacking flash-memory cells, the density, utility, and low cost of 3D flash memory made it popular in applications from smartphones to automobiles to data centers. However, certain misconceptions about 3D flash still dominate the industry. There are three points we’d like to emphasize this month to help you make an informed decision as you evaluate your memory options:
- Not all 3D NAND flash memory is equal.
3D flash is not a technology that’s limited to a specific temperature range or application. It’s a versatile tech with a range of solutions that support different use cases, temperature ranges, levels of reliability, and levels of performance. Every emphasis comes with a drawback, which is why there are unique flash-memory products and SSD solutions to support client, data center, and enterprise markets. Consider what your product most prizes: reliability, performance, power, or cost. Your supplier can guide you to the correct type of 3D flash memory from there. - 2D flash memory (and earlier 3D memory) still has value.
It’s true that 3D is today’s dominant flash-memory architecture. However, applications that only require small densities are still making cost-effective use of 2D floating-gate SLC flash memory in densities such as 1, 2, or 4 GB of flash. Other applications may only require 4 or 8 GB of MLC floating-gate eMMC. The latest 3D flash memory, by contrast, is typically manufactured in die densities of 256 or 512 GB — which achieve the best cost per gigabyte due to the way they’re designed and manufactured. It’s likely that future 3D flash generations will see increases in the minimum die density supported, and this means that numerous older flash generations will continue to be in demand based on use cases and density requirements. Low-density applications have no reason to opt for the extremely high minimums of current 3D flash.
- More layers are not always best for the bottom line.
For each generation of 3D flash memory, the optimal number of layers will depend on the unique supplier. Some suppliers might have 64 layers rather than 72 layers. In a later generation, one supplier could rest on a 92-layer design vs. others with a 96-layer design.
Every supplier is trying to squeeze the most out of each generation with the least capital investment. Each layer adds incremental costs but also boosts density per wafer. This is why every supplier is experimenting and discovering their own ideal balance. As layer counts rise, it’s likely we’ll continue to see even more variety.
Manufacturers Leverage Inventory Management ABCs to Reduce the Cost of Doing Business
Managing inventory is complex, and inefficient methods can become an enormous cost sink. With the tightening of budgets in today’s volatile supply chain, many manufacturers are seeking a way to control costs.
It’s commonly cited that 70-80% of a company’s annual consumption value comes from only about 10-20% of all its inventory. This is often the result of having too many slow-selling products on hand and not enough of the items customers want most.
Manufacturers today are growing more familiar with this concept and leaning into what’s called the “A-B-C Method” of inventory management. Essentially, you break down your inventory into three tiers:
- Category A: The highest-consumption-value items, likely about 20% of inventory.
- Category B: Items that comprise 15-20% of annual consumption value, but about 30% of all inventory.
- Category C: Items that account for less than 5% of the annual consumption value, and about 50% of the total inventory.
Once your inventory has been segmented in this way, it’s much easier to assess which products generate the most profits, and which ones you can deprioritize because they are less profitable. A focus on sourcing the inventory that’s most likely to pay off saves a lot of money in the long run. This is a tried and true approach, but it’s only one example of what’s possible.
Today’s manufacturers are also picking up efficiency tips from other sectors. For example, the U.S. army recently recycled 15 tons of expired documents in Panzer Kaserne, Germany, which resulted in nearly 1,000 wooden pallets full of paperwork. Military leaders were able to repurpose the pallets by integrating them back into the supply chain, saving more than €27,000. Not only did this eliminate the cost of disposing of them, but it helped the organization that received them to send semi-perishables to commissaries across Europe without buying new pallets.
Working to Make Printed Circuit Board Production More Environmentally Friendly
It’s no secret that the manufacturing process to create printed circuit boards can carry high environmental costs. Reducing pollution and operating in a more “green” fashion can help companies polish their public image as well as satisfy stockholders who are concerned about the state of our natural resources.
And relying on more environmentally friendly solutions and supply chains can help companies when it comes to recruiting new employees, who are often concerned about the impact their work will have on the world. A case in point is a Swedish company called Sigma MECER. It is working to follow the ideals of “reduce, reuse, and recycle” in the PCB industry. Sigma MECER has created an etchant regeneration system designed to facilitate chemical recycling in a closed-loop process.
The byproducts of this system are rinsed water and pure copper plates, which fulfill the idea of recycling. It works with acidic and alkaline etchant closed-loop regeneration facilities. Companies using such a system can reduce their consumption of HCI by 95%. What’s more, there is no longer a need for replenishing alkaline etchant. And since the copper plates that result are 99.995% pure, they are suitable for being put on sale as anodic grade copper.
Stay Up-to-Date on Semiconductor News With Sensible Micro
It’s important to stay on top of developments in electronic component news. However, the chances are good that you and your team have little time to spare, given your current job responsibilities. To make sure that you and fellow stakeholders in your organization don’t miss a thing, visit this blog on a regular basis so that you can stay informed with Sensible Micro.
Sources:
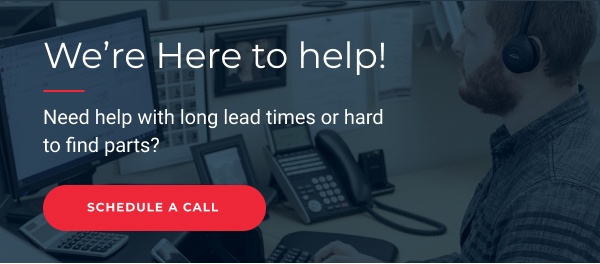